En la vida cotidiana, un diseñador de productos o un gerente de productos necesita métodos adecuados para un producto sin errores. Para hacerlo posible, existen varios métodos. Uno es DFMEA; otro es PFMEA. La forma completa de DFMEA es el modo de falla de diseño y el análisis de efectos.
Se centra principalmente en problemas relacionados con el diseño. Otro es PFMEA, que es el modo de falla del proceso y el análisis del efecto. Se utiliza en el análisis de procesos.
DFMEA y PFMEA pertenecen a FMEA (análisis de modo y efecto de falla), un tipo de análisis realizado para crear un error-producto gratuito con un diseño decente. DFMEA debe componer cada parte ensamblada utilizada durante el diseño de un producto.
Y se accede a todo el proceso por el método FMEA.
Puntos clave
- DFMEA (Análisis de modo y efectos de fallas de diseño) identifica y previene sistemáticamente las fallas de diseño, mientras que PFMEA (Análisis de modos y efectos de fallas de procesos) tiene como objetivo prevenir fallas de procesos durante la fabricación o el ensamblaje.
- El enfoque principal de DFMEA está en el diseño del producto, asegurando que el diseño cumpla con los requisitos del cliente e identificando posibles modos de falla. Por el contrario, PFMEA tiene como objetivo identificar posibles modos de falla en el proceso de fabricación o ensamblaje.
- DFMEA implica analizar las posibles consecuencias de un modo de falla y evaluar su gravedad, probabilidad de ocurrencia y capacidad de detección. Por el contrario, PFMEA implica identificar los posibles modos de falla, sus causas y sus efectos en el proceso y priorizar el riesgo en función de la gravedad, la probabilidad de ocurrencia y la capacidad de detección.
DFMEA frente a PFMEA
DFMEA se utiliza durante la fase de diseño de un producto o proceso para identificar posibles modos de falla y sus posibles efectos y determinar la probabilidad y la gravedad de esas fallas. DFMEA tiene como objetivo prevenir fallas potenciales antes de que ocurran al realizar mejoras en el diseño. PFMEA se utiliza durante el proceso de fabricación para identificar fallas potenciales y sus efectos y determinar la probabilidad y la gravedad de esas fallas. PFMEA tiene como objetivo identificar y prevenir fallas que pueden ocurrir durante la Production proceso y mejorar la calidad y confiabilidad del producto o proceso.
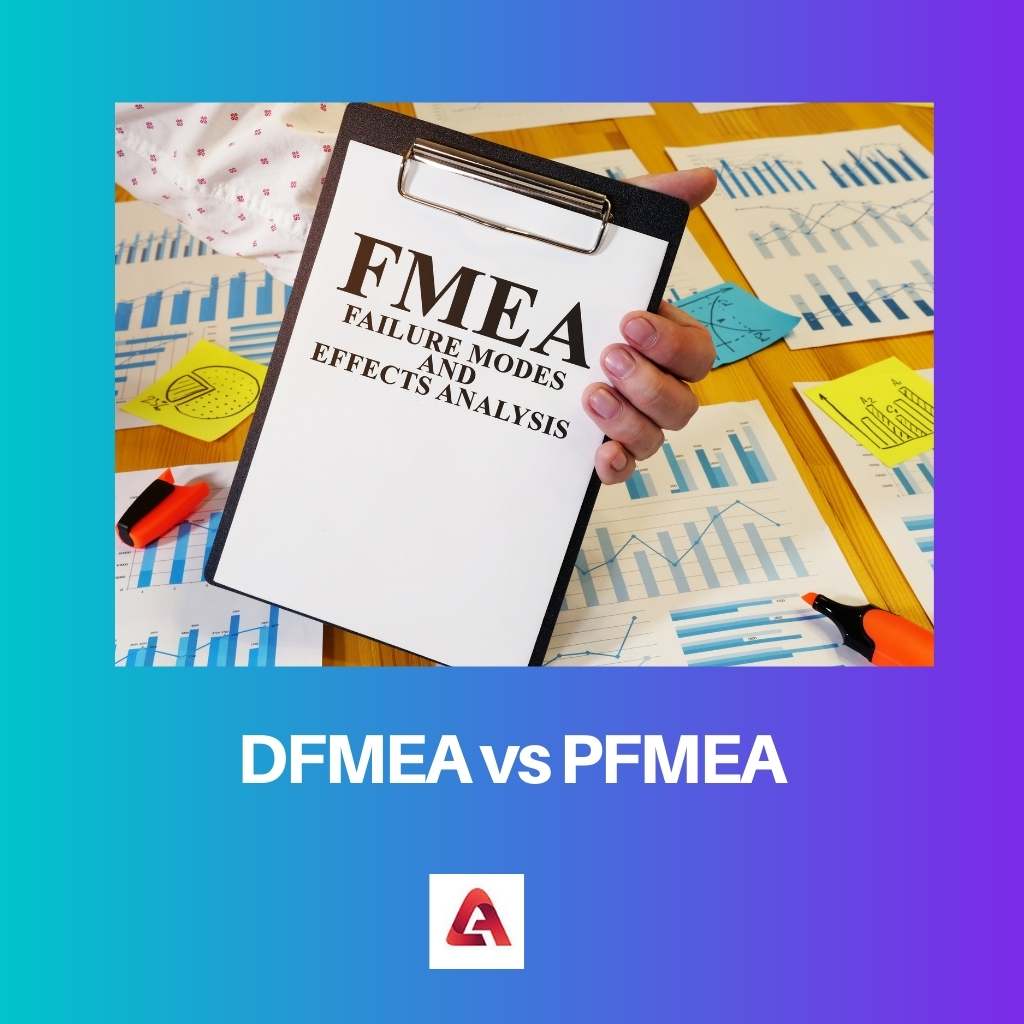
DFMEA (análisis de modo y efecto de falla de diseño) encuentra y resuelve errores. Captura todos los problemas relacionados con el diseño y encuentra una solución completa para ellos.
Ayuda a un diseñador a encontrar la pieza correcta que se puede utilizar en la construcción de un producto.
PFMEA es un análisis de modo y efecto de falla de proceso. Como su nombre lo muestra, el proceso está conectado al análisis del modo de falla del proceso. Ayuda a reconocer la raíz de la falla del proceso, y luego resuelve la causa. Es una herramienta integrada para comprobar todo tipo de posibles fallos.
Tabla de comparación
Parámetros de comparación | DFMEA | AMEF |
---|---|---|
Definición | DFMEA es un método de análisis para el modo de falla del diseño y el análisis del efecto. | PFMEA es un método de análisis de procesos para el modo de falla de procesos y el análisis de efectos. |
énfasis | Enfatiza principalmente los errores de diseño del producto. | Se centra principalmente en el análisis de procesos durante la fabricación del producto. |
Objetivo | Su objetivo principal es descubrir todos los errores de diseño y las consecuencias del problema. | Su principal objetivo es analizar el proceso, cubrir todos los posibles fallos y solucionarlos. |
Categoría de método | Viene bajo modo de falla y análisis de efecto (FMEA). | También se incluye en el método de análisis de modo y efecto de falla (FMEA) |
Caracteristicas claves | Maneja los métodos de salida y su análisis. | Administra los métodos de entrada y su análisis. |
¿Qué es DFMEA?
DFMEA es un método que se utiliza para analizar el diseño de un producto o sistema. Analiza el proceso de salida e informa de todas las consecuencias que pueden ocurrir si se ensamblan piezas no adecuadas durante el diseño de un sistema o producto.
Viene bajo modo de falla y análisis de efecto (FMEA).
DFMEA gestiona principalmente el análisis de salida relacionado con la apariencia del producto. Es un método utilizado en el diseño de productos que encuentra la posibilidad de un defecto de diseño o construcción en la implementación real de un producto.
Si se contrarresta algún error, los diseñadores intentan resolver la causa aplicando una solución rápida.
Recoge las funciones esenciales en un diseño y luego examina el probable origen del colapso de un sistema o producto.
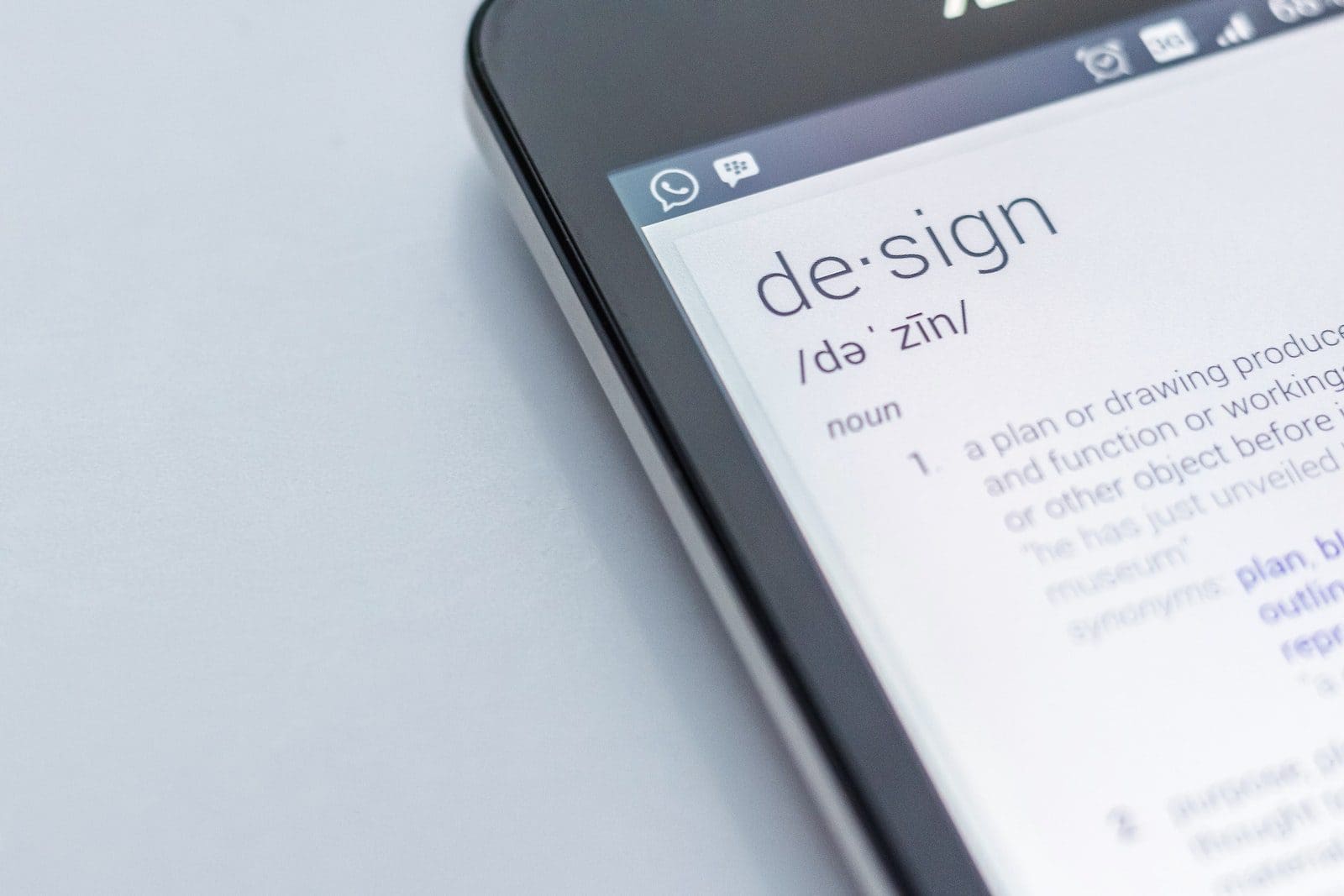
¿Qué es PFMEA?
PFMEA es un método de análisis para el modo de falla del proceso y el análisis del efecto. Este método también se incluye en el proceso de análisis de modo y efecto de falla. Detecta todos los posibles errores que se cometen durante el procesamiento de un producto o sistema.
Es un método utilizado en el proceso de fabricación del producto que encuentra la posibilidad de un defecto de procesamiento y sus efectos posteriores con la ayuda de un análisis de informe detallado.
Es una herramienta integrada utilizada por todo tipo de instituciones para comprobar diferentes posibles errores que pueden causar la falla de un sistema o la falla de un producto. También detecta la causa de la falla mediante la recopilación de datos. Se inicia o ejecuta antes de procesar cualquier producto.
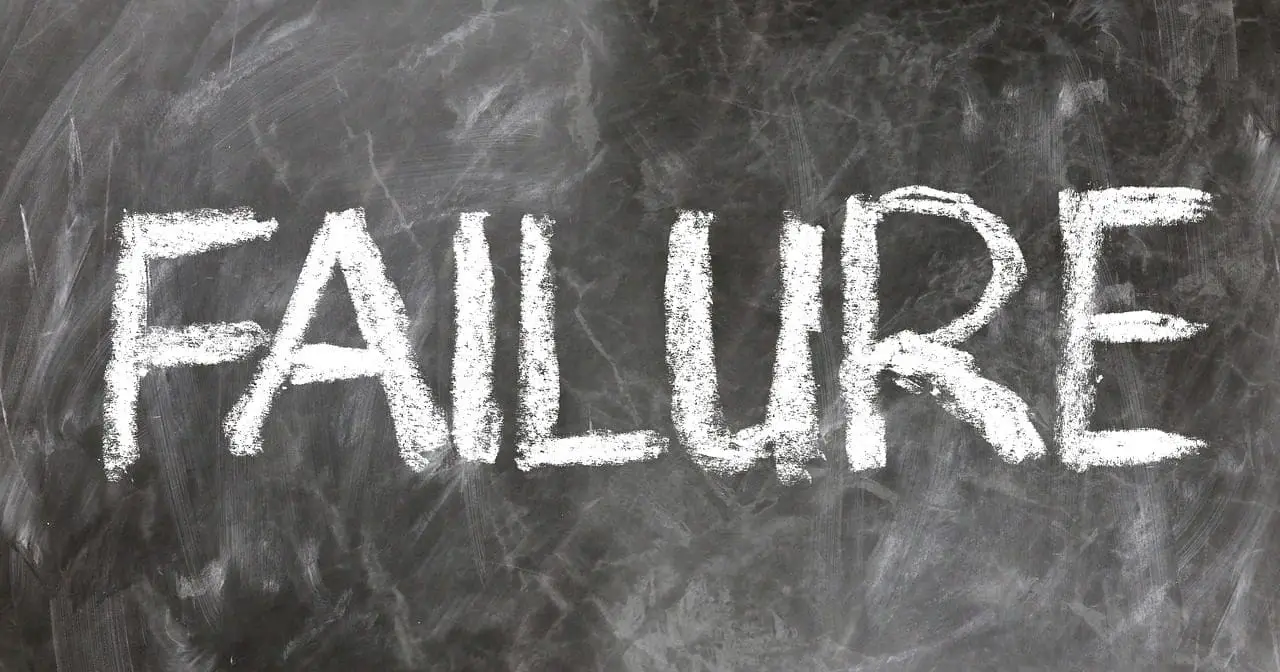
Principales diferencias entre DFMEA y PFMEA
- DFMEA está completamente relacionado con cuestiones de diseño. Es un método utilizado para analizar cualquier error relacionado con la representación de un sistema o producto. Y PFMEA está completamente relacionado con el proceso con el que funciona un producto o un sistema. Analiza cuestiones relacionadas con la tramitación.
- DFMEA enfatiza principalmente los problemas relacionados con el diseño de un producto, y PFMEA enfatiza el procesamiento del producto.
- PFMEA se inicia o ejecuta antes de procesar cualquier producto. Y DFMEA se inicia o ejecuta antes de diseñar cualquier producto o sistema.
- En DFMEA, los elementos de riesgo pueden provocar un cambio tanto en el diseño como en el procesamiento. En PFMEA, los elementos de riesgo pueden causar un cambio solo en el procesamiento.
- DFMEA reduce el riesgo de falla en el proceso de diseño y PFMEA reduce el riesgo de falla en el proceso de producción al proporcionar un análisis de informe detallado.
- https://www.sciencedirect.com/science/article/pii/S0957417409007039
- https://www.sciencedirect.com/science/article/pii/S0924013603005429
Última actualización: 11 de junio de 2023

Sandeep Bhandari tiene una Licenciatura en Ingeniería Informática de la Universidad de Thapar (2006). Tiene 20 años de experiencia en el campo de la tecnología. Tiene un gran interés en varios campos técnicos, incluidos los sistemas de bases de datos, las redes informáticas y la programación. Puedes leer más sobre él en su página de biografía.
Este es un artículo increíblemente informativo sobre DFMEA y PFMEA. Explica detalladamente las diferencias entre los dos y la importancia de cada uno en el proceso de desarrollo del producto. Siento que he adquirido mucha información al leer esto.
No podría estar más de acuerdo, Bethany. Este artículo ciertamente ha profundizado mi comprensión de estos conceptos.
La explicación detallada de DFMEA y PFMEA fue esclarecedora, pero podría beneficiarse de ejemplos del mundo real para mejorar la comprensión.
Estás en lo cierto, Jrichards. Sin duda, los ejemplos reforzarían la claridad y aplicabilidad de estos métodos.
Este artículo parece simplificar demasiado el papel de DFMEA y PFMEA en el desarrollo de productos. Hay más complejidades involucradas que no se abordan adecuadamente aquí.
También me pareció algo deficiente abordar el alcance completo de estos métodos de análisis, Irichardson.
Comparto tu perspectiva, Irichardson. El artículo parece ofrecer una visión limitada de estos métodos.
El artículo presenta una descripción general completa de DFMEA y PFMEA, pero podría profundizar en los aspectos procesales y estudios de casos detallados.
Estoy de acuerdo contigo, Cris. Los casos del mundo real proporcionarían información práctica sobre la aplicación de estos métodos.
Aunque el artículo es un recurso valioso, parece carecer de una exploración en profundidad de las aplicaciones de estos métodos en diferentes industrias.
Estoy completamente de acuerdo contigo, Gary. Las aplicaciones específicas de DFMEA y PFMEA en todas las industrias habrían sido enriquecedoras.
Si bien aprecio la información detallada proporcionada en este artículo, creo que el énfasis en estos métodos descuida otros procesos importantes de garantía de calidad en el desarrollo de productos.
Ese es un punto válido, Evie. Sería beneficioso explorar la integración de estos métodos con otros procesos de garantía de calidad.
Estoy de acuerdo, Evie. Si bien DFMEA y PFMEA son valiosos, deberían ser parte de una estrategia de gestión de calidad más amplia.
La comparación entre DFMEA y PFMEA dejó muy claras las diferencias. ¡Es una aproximación humorística a un campo técnico!
Absolutamente, Vhall. No es que veamos un toque de ingenio en los artículos técnicos.
No pude evitar reírme de cómo la tabla de comparación simplificaba conceptos tan complejos.
La tabla comparativa completa entre DFMEA y PFMEA fue particularmente útil. Aclara las distinciones y beneficios de cada método de manera muy efectiva.
Absolutamente, Carlota. Es una gran referencia para cualquiera que busque comprender estos métodos en detalle.
Si bien el contenido es informativo, el tono del artículo podría percibirse como demasiado técnico. Agregar un toque de accesibilidad mejoraría su atractivo para una audiencia más amplia.
Estoy de acuerdo, Lwalker. Comunicar estos conceptos de una manera más accesible haría que este contenido fuera más inclusivo.
Absolutamente, Lwalker. Un equilibrio entre el detalle técnico y la accesibilidad es importante en artículos de esta naturaleza.
Las distinciones entre DFMEA y PFMEA se articularon claramente, proporcionando una comprensión coherente. Es encomiable cómo se resaltaron las diferencias clave.
No podría estar más de acuerdo, Simpson. El artículo hizo un trabajo fantástico al resaltar los matices entre los dos métodos.
Absolutamente, Simpson. La claridad a la hora de diferenciar estos métodos fue sorprendente.