Dalam kehidupan sehari-hari, seorang desainer produk atau manajer produk memerlukan metode yang sesuai untuk produk bebas kesalahan. Untuk membuatnya mungkin, ada beberapa metode. Salah satunya adalah DFMEA; lainnya adalah PFMEA. Bentuk lengkap dari DFMEA adalah mode kegagalan desain dan analisis efek.
Ini terutama difokuskan pada masalah yang berkaitan dengan desain. Lainnya adalah PFMEA yang merupakan mode kegagalan proses dan analisis efek. Ini digunakan dalam analisis proses.
DFMEA dan PFMEA berada di bawah FMEA (failure mode and effect analysis), sejenis analisis yang dilakukan untuk membuat kesalahan-produk gratis dengan desain yang layak. DFMEA harus menyusun setiap bagian rakitan yang digunakan selama desain produk.
Dan seluruh proses diakses dengan metode FMEA.
Pengambilan Kunci
- DFMEA (Mode Kegagalan Desain dan Analisis Efek) secara sistematis mengidentifikasi dan mencegah kegagalan desain, sedangkan PFMEA (Mode Kegagalan Proses dan Analisis Efek) bertujuan untuk mencegah kegagalan proses selama pembuatan atau perakitan.
- Fokus utama DFMEA adalah pada desain produk, memastikan bahwa desain tersebut memenuhi persyaratan pelanggan dan mengidentifikasi mode kegagalan potensial. Sebaliknya, PFMEA bertujuan untuk mengidentifikasi mode kegagalan potensial dalam proses pembuatan atau perakitan.
- DFMEA melibatkan analisis konsekuensi potensial dari mode kegagalan dan mengevaluasi tingkat keparahannya, probabilitas kejadian, dan kemampuan deteksi. Sebaliknya, PFMEA melibatkan identifikasi mode kegagalan potensial, penyebabnya, dan pengaruhnya terhadap proses dan memprioritaskan risiko berdasarkan tingkat keparahan, probabilitas kejadian, dan kemampuan deteksi.
DFMEA vs PFMEA
DFMEA digunakan selama fase desain suatu produk atau proses untuk mengidentifikasi mode kegagalan potensial dan efek potensialnya serta menentukan kemungkinan dan tingkat keparahan kegagalan tersebut. DFMEA bertujuan untuk mencegah potensi kegagalan sebelum terjadi dengan melakukan perbaikan desain. PFMEA digunakan selama proses pembuatan untuk mengidentifikasi potensi kegagalan dan pengaruhnya serta menentukan kemungkinan dan tingkat keparahan kegagalan tersebut. PFMEA bertujuan untuk mengidentifikasi dan mencegah kegagalan yang mungkin terjadi selama produksi memproses dan meningkatkan kualitas dan keandalan produk atau proses.
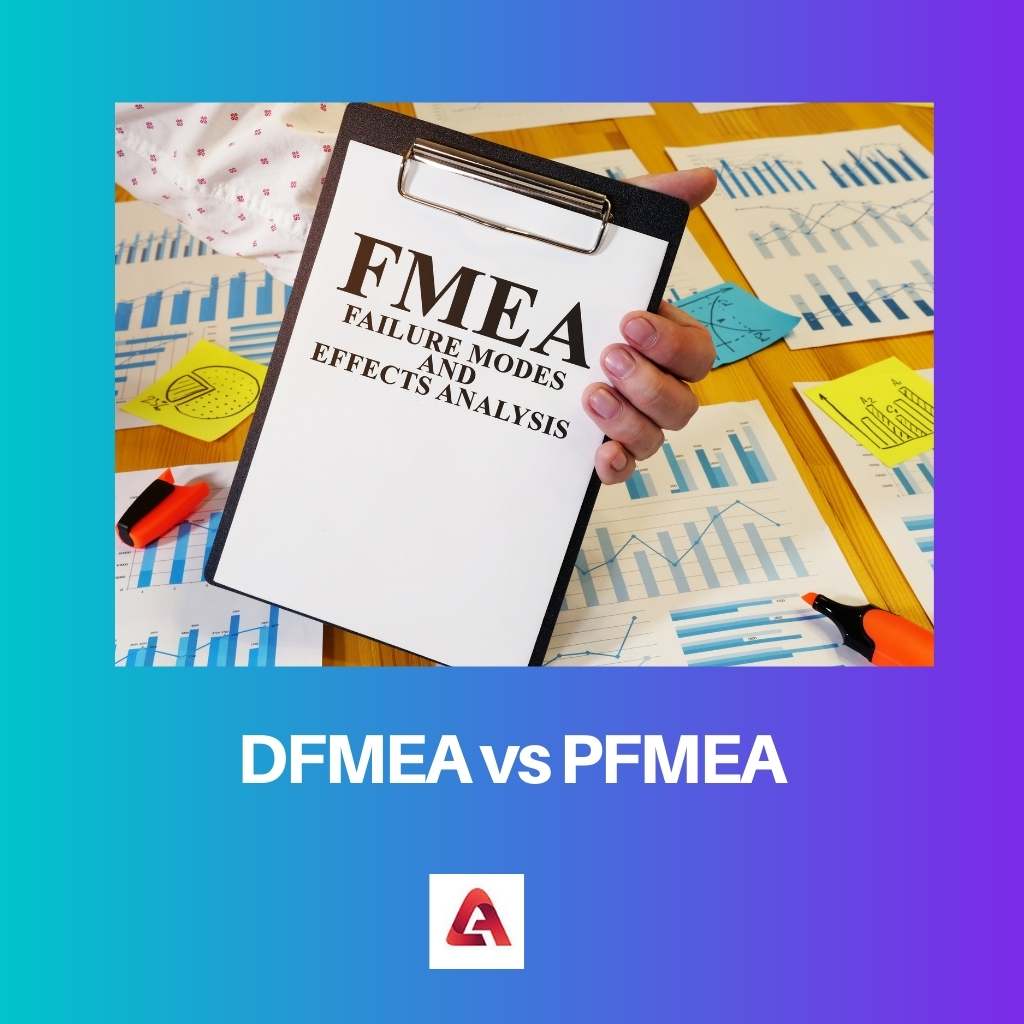
DFMEA (mode kegagalan desain dan analisis efek) menemukan dan menyelesaikan kesalahan. Itu menangkap semua masalah yang terkait dengan desain dan menemukan solusi lengkap untuk mereka.
Ini membantu seorang desainer menemukan bagian yang tepat yang dapat digunakan dalam membangun suatu produk.
PFMEA adalah mode kegagalan proses dan analisis efek. Seperti namanya, proses terhubung ke analisis mode kegagalan proses. Ini membantu untuk mengenali akar dari kegagalan proses, dan kemudian menyelesaikan penyebabnya. Ini adalah alat terintegrasi untuk memeriksa semua jenis kemungkinan kegagalan.
Tabel perbandingan
Parameter Perbandingan | DFMEA | PFMEA |
---|---|---|
Definisi | DFMEA adalah metode analisis untuk mode kegagalan desain dan analisis efek. | PFMEA adalah metode analisis proses untuk mode kegagalan proses dan analisis efek. |
Penekanan | Ini terutama menekankan kesalahan desain produk. | Ini terutama berfokus pada analisis proses selama pembuatan produk. |
Tujuan | Tujuan utamanya adalah untuk mengetahui semua kesalahan desain dan konsekuensi dari masalah tersebut. | Tujuan utamanya adalah untuk menganalisis proses, menutupi semua kemungkinan kegagalan, dan menyelesaikannya. |
Kategori metode | Muncul di bawah mode kegagalan dan analisis efek (FMEA). | Itu juga datang di bawah metode mode kegagalan dan analisis efek (FMEA) |
Karakteristik utama | Mengelola metode keluaran dan analisisnya. | Mengelola metode input dan analisisnya. |
Apa itu DFMEA?
DFMEA adalah metode yang digunakan untuk menganalisis desain suatu produk atau sistem. Ini menganalisis proses keluaran dan melaporkan semua konsekuensi yang dapat terjadi jika bagian yang tidak sesuai dipasang selama perancangan sistem atau produk.
Muncul di bawah mode kegagalan dan analisis efek (FMEA).
DFMEA terutama mengelola analisis keluaran yang berkaitan dengan tampilan produk. Ini adalah metode yang digunakan dalam perancangan produk yang menemukan kemungkinan cacat desain atau konstruksi dalam implementasi produk yang sebenarnya.
Jika ada kesalahan yang diatasi, para perancang mencoba menyelesaikan penyebabnya dengan menerapkan perbaikan cepat.
Ini mengumpulkan fungsi-fungsi penting dalam suatu desain dan kemudian memeriksa kemungkinan asal runtuhnya suatu sistem atau produk.
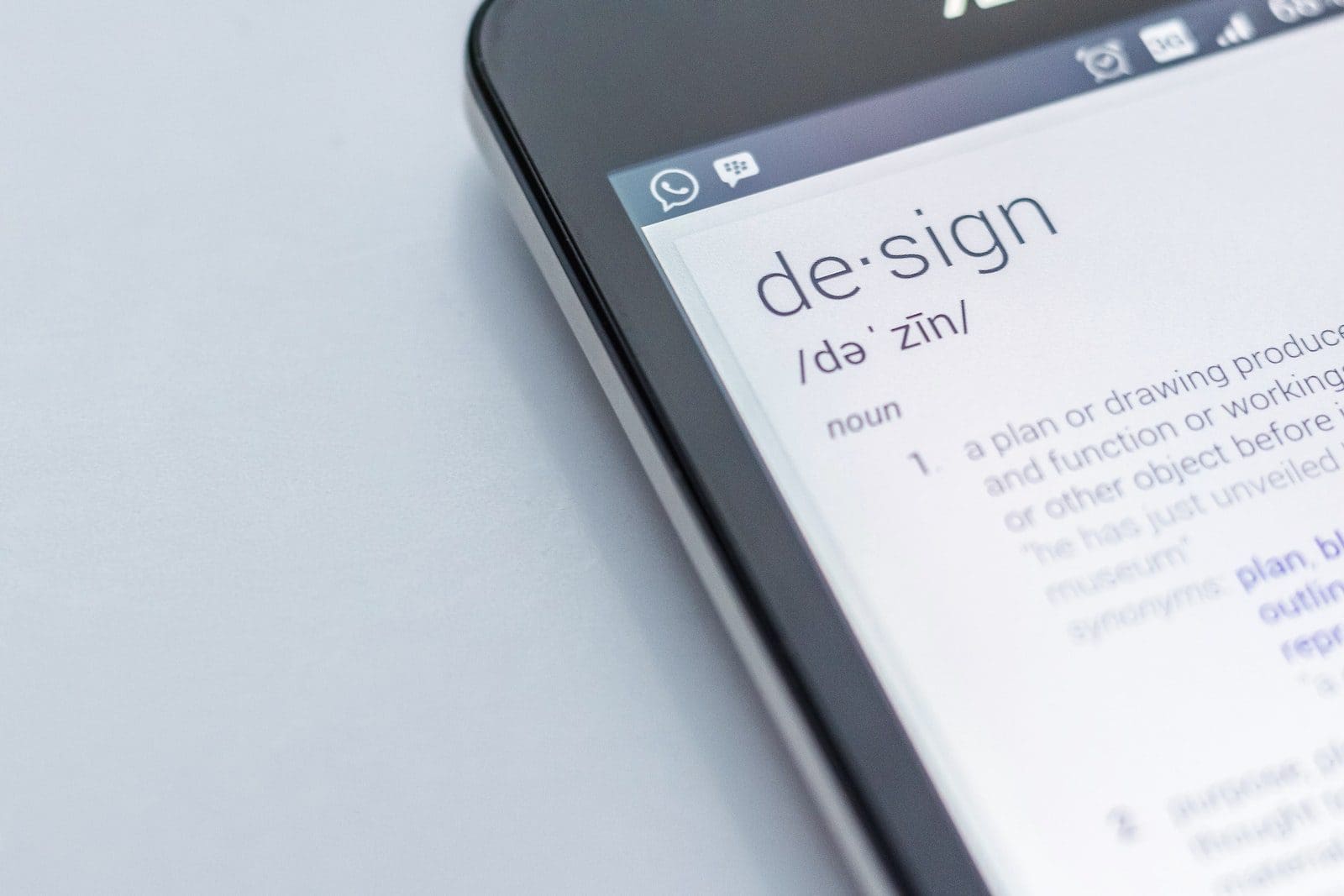
Apa itu PFMEA?
PFMEA adalah metode analisis untuk mode kegagalan proses dan analisis efek. Metode ini juga termasuk mode kegagalan dan proses analisis efek. Ini mendeteksi semua kemungkinan kesalahan yang dibuat selama pemrosesan suatu produk atau sistem.
Ini adalah metode yang digunakan dalam proses pembuatan produk yang menemukan kemungkinan cacat pemrosesan dan efek sampingnya dengan bantuan analisis laporan terperinci.
Ini adalah alat terintegrasi yang digunakan oleh semua jenis institusi untuk memeriksa berbagai kemungkinan kesalahan yang dapat menyebabkan kegagalan sistem atau kegagalan produk. Itu juga mendeteksi penyebab kegagalan dengan mengumpulkan data. Itu dimulai atau dieksekusi sebelum memproses produk apa pun.
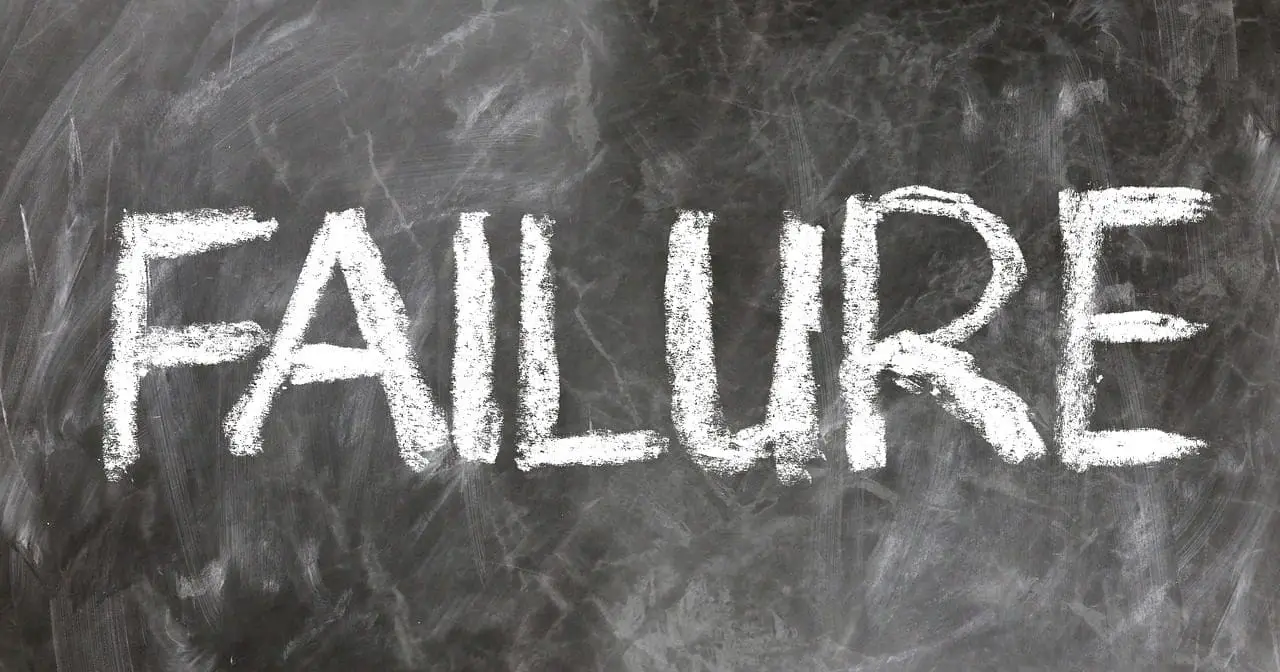
Perbedaan Utama Antara DFMEA dan PFMEA
- DFMEA sepenuhnya terkait dengan masalah desain. Ini adalah metode yang digunakan untuk menganalisis kesalahan apa pun yang terkait dengan representasi sistem atau produk. Dan PFMEA sepenuhnya terkait dengan proses dengan bantuan produk atau sistem yang berfungsi. Ini menganalisis masalah yang terkait dengan pemrosesan.
- DFMEA terutama menekankan masalah yang berhubungan dengan desain suatu produk, dan PFMEA menekankan pemrosesan produk.
- PFMEA dimulai atau dijalankan sebelum memproses produk apa pun. Dan DFMEA dimulai atau dijalankan sebelum merancang produk atau sistem apa pun.
- Di DFMEA, item risiko dapat menyebabkan perubahan baik dalam desain maupun pemrosesan. Di PFMEA, item risiko dapat menyebabkan perubahan hanya dalam pemrosesan.
- DFMEA mengurangi resiko kegagalan dalam proses desain, dan PFMEA mengurangi resiko kegagalan dalam proses produksi dengan menyediakan analisis laporan yang detail.
- https://www.sciencedirect.com/science/article/pii/S0957417409007039
- https://www.sciencedirect.com/science/article/pii/S0924013603005429
Terakhir Diperbarui : 11 Juni 2023

Sandeep Bhandari meraih gelar Bachelor of Engineering in Computers dari Thapar University (2006). Beliau memiliki pengalaman selama 20 tahun di bidang teknologi. Dia memiliki minat dalam berbagai bidang teknis, termasuk sistem database, jaringan komputer, dan pemrograman. Anda dapat membaca lebih lanjut tentang dia di nya halaman bio.
Ini adalah artikel yang sangat informatif tentang DFMEA dan PFMEA. Ini menjelaskan secara menyeluruh perbedaan antara keduanya dan pentingnya masing-masing dalam proses pengembangan produk. Saya merasa mendapat banyak wawasan dengan membaca ini.
Saya sangat setuju, Bethany. Artikel ini tentunya memperdalam pemahaman saya tentang konsep-konsep tersebut.
Penjelasan rinci tentang DFMEA dan PFMEA sangat mendalam, namun dapat memanfaatkan contoh-contoh dunia nyata untuk meningkatkan pemahaman.
Anda tepat, Jrichards. Contoh-contoh tentu saja akan meningkatkan kejelasan dan penerapan metode-metode ini.
Artikel ini sepertinya terlalu menyederhanakan peran DFMEA dan PFMEA dalam pengembangan produk. Ada lebih banyak kompleksitas yang terlibat yang tidak dibahas secara memadai di sini.
Saya juga merasa ada kekurangan dalam membahas keseluruhan cakupan metode analisis ini, Irichardson.
Saya berbagi perspektif Anda, Irichardson. Artikel tersebut tampaknya memberikan pandangan sempit mengenai metode ini.
Artikel ini menyajikan gambaran komprehensif tentang DFMEA dan PFMEA, namun dapat menggali lebih dalam aspek prosedural dan studi kasus yang terperinci.
Aku setuju denganmu, Kris. Kasus-kasus di dunia nyata akan memberikan wawasan praktis mengenai penerapan metode-metode ini.
Meskipun artikel ini merupakan sumber yang berharga, tampaknya artikel ini kurang mengeksplorasi secara mendalam penerapan metode ini di berbagai industri.
Saya sepenuhnya setuju dengan Anda, Gary. Penerapan spesifik DFMEA dan PFMEA di seluruh industri akan semakin memperkaya.
Meskipun saya menghargai informasi rinci yang diberikan dalam artikel ini, saya merasa bahwa penekanan pada metode ini mengabaikan proses jaminan kualitas penting lainnya dalam pengembangan produk.
Itu poin yang valid, Evie. Akan bermanfaat untuk mengeksplorasi integrasi metode ini dengan proses QA lainnya.
Aku setuju, Evie. Meskipun DFMEA dan PFMEA bermanfaat, keduanya harus menjadi bagian dari strategi manajemen mutu yang lebih luas.
Perbandingan antara DFMEA dan PFMEA membuat perbedaannya menjadi sangat jelas. Ini adalah pendekatan lucu untuk bidang teknis!
Tentu saja, Vhall. Kita tidak melihat adanya sentuhan kecerdasan dalam artikel teknis.
Saya tidak bisa menahan tawa melihat bagaimana tabel perbandingan menyederhanakan konsep rumit tersebut.
Tabel perbandingan komprehensif antara DFMEA dan PFMEA sangat membantu. Ini menjelaskan perbedaan dan manfaat masing-masing metode dengan sangat efektif.
Tentu saja, Charlotte. Ini adalah referensi bagus bagi siapa pun yang ingin memahami metode ini secara mendetail.
Meskipun isinya informatif, nada artikelnya mungkin dianggap terlalu teknis. Menambahkan sentuhan aksesibilitas akan meningkatkan daya tariknya bagi khalayak yang lebih luas.
Saya setuju, Lwalker. Mengkomunikasikan konsep-konsep ini dengan cara yang lebih mudah diakses akan menjadikan konten ini lebih inklusif.
Tentu saja, Lwalker. Keseimbangan antara detail teknis dan aksesibilitas penting dalam artikel semacam ini.
Perbedaan antara DFMEA dan PFMEA diartikulasikan dengan jelas, sehingga memberikan pemahaman yang koheren. Sungguh terpuji bagaimana perbedaan-perbedaan utama disoroti.
Saya sangat setuju, Simpson. Artikel tersebut berhasil menyoroti perbedaan antara kedua metode tersebut.
Tentu saja, Simpson. Kejelasan dalam membedakan metode-metode ini sangat mencolok.