In het dagelijkse leven heeft een productontwerper of een productmanager geschikte methodes nodig voor een foutloos product. Om dit mogelijk te maken, zijn er verschillende methodes. Een daarvan is DFMEA; een andere is PFMEA. De volledige vorm van DFMEA is ontwerpfoutmodus en effectanalyse.
Het is vooral gericht op problemen met betrekking tot ontwerp. Een andere is PFMEA, de procesfoutmodus en effectanalyse. Het wordt gebruikt in procesanalyse.
DFMEA en PFMEA vallen onder FMEA (failure mode and effect analysis), een soort analyse die wordt uitgevoerd om een fout-gratis product met een degelijk ontwerp. DFMEA moet elk geassembleerd onderdeel vormen dat tijdens het ontwerp van een product wordt gebruikt.
En het hele proces is toegankelijk via de FMEA-methode.
Key Takeaways
- DFMEA (Design Failure Mode and Effects Analysis) identificeert en voorkomt ontwerpfouten systematisch, terwijl PFMEA (Process Failure Mode and Effects Analysis) gericht is op het voorkomen van procesfouten tijdens productie of montage.
- De primaire focus van DFMEA ligt op productontwerp, ervoor zorgen dat het ontwerp voldoet aan de eisen van de klant en het identificeren van mogelijke faalwijzen. PFMEA daarentegen heeft tot doel potentiële faalwijzen in het fabricage- of assemblageproces te identificeren.
- DFMEA omvat het analyseren van de mogelijke gevolgen van een storingsmodus en het evalueren van de ernst, de waarschijnlijkheid van optreden en het detectievermogen. PFMEA daarentegen omvat het identificeren van mogelijke faalwijzen, hun oorzaken en hun effecten op het proces en het prioriteren van het risico op basis van ernst, waarschijnlijkheid van optreden en detectievermogen.
DFMEA versus PFMEA
DFMEA wordt gebruikt tijdens de ontwerpfase van een product of proces om mogelijke faalwijzen en hun mogelijke effecten te identificeren en de waarschijnlijkheid en ernst van die storingen te bepalen. DFMEA streeft ernaar mogelijke storingen te voorkomen voordat ze zich voordoen door ontwerpverbeteringen aan te brengen. PFMEA wordt tijdens het fabricageproces gebruikt om mogelijke storingen en hun effecten te identificeren en de waarschijnlijkheid en ernst van die storingen te bepalen. PFMEA heeft tot doel storingen die kunnen optreden tijdens de uitvoering te identificeren en te voorkomen productie verwerken en de kwaliteit en betrouwbaarheid van het product of proces verbeteren.
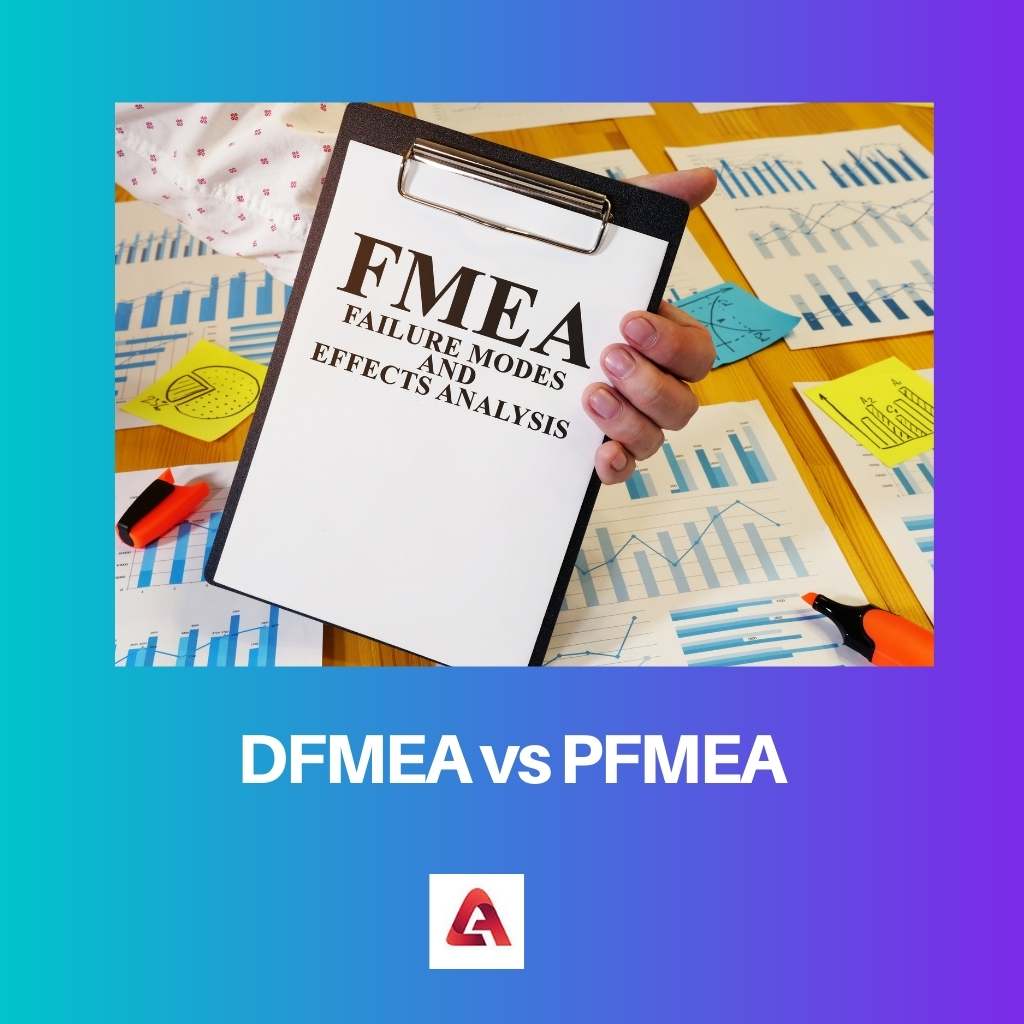
DFMEA (design failure mode and effect analysis) vindt en lost fouten op. Het legt alle problemen met betrekking tot ontwerp vast en vindt er een complete oplossing voor.
Het helpt een ontwerper het juiste onderdeel te vinden dat kan worden gebruikt bij het bouwen van een product.
PFMEA is een processtoringsmodus- en effectanalyse. Zoals de naam laat zien, is het proces verbonden met de procesfoutmodusanalyse. Het helpt om de wortel van het mislukken van het proces, en dan lost het de oorzaak op. Het is een geïntegreerde tool voor het controleren van alle soorten mogelijke storingen.
Vergelijkingstabel
Parameters van vergelijking: | DFMEA | PFMEA |
---|---|---|
Definitie | DFMEA is een analysemethode voor ontwerpfout- en effectanalyse. | PFMEA is een procesanalysemethode voor procesfalen en effectanalyse. |
nadruk | Het legt vooral de nadruk op productontwerpfouten. | Het richt zich voornamelijk op procesanalyse tijdens het maken van producten. |
Objectief | Het belangrijkste doel is om alle ontwerpfouten en de gevolgen van het probleem te achterhalen. | Het belangrijkste doel is om het proces te analyseren, alle mogelijke fouten te dekken en op te lossen. |
Methode categorie | Het valt onder de faalmodus en effectanalyse (FMEA). | Het valt ook onder de methode van faalmodus en effectanalyse (FMEA) |
Sleuteleigenschappen | Beheert uitvoermethoden en hun analyse. | Beheert invoermethoden en hun analyse. |
Wat is DFMEA?
DFMEA is een methode die wordt gebruikt om het ontwerp van een product of systeem te analyseren. Het analyseert het uitvoerproces en rapporteert alle gevolgen die kunnen optreden als tijdens het ontwerpen van een systeem of product niet passende onderdelen worden samengesteld.
Het valt onder de faalmodus en effectanalyse (FMEA).
DFMEA beheert voornamelijk de outputanalyse die betrekking heeft op het uiterlijk van het product. Het is een methode die wordt gebruikt bij het ontwerpen van producten die de mogelijkheid van een ontwerp- of constructiefout in een daadwerkelijke productimplementatie vindt.
Als een fout wordt tegengegaan, proberen de ontwerpers de oorzaak op te lossen door een snelle oplossing toe te passen.
Het verzamelt de essentiële functies in een ontwerp en onderzoekt vervolgens de waarschijnlijke oorsprong van het instorten van een systeem of product.
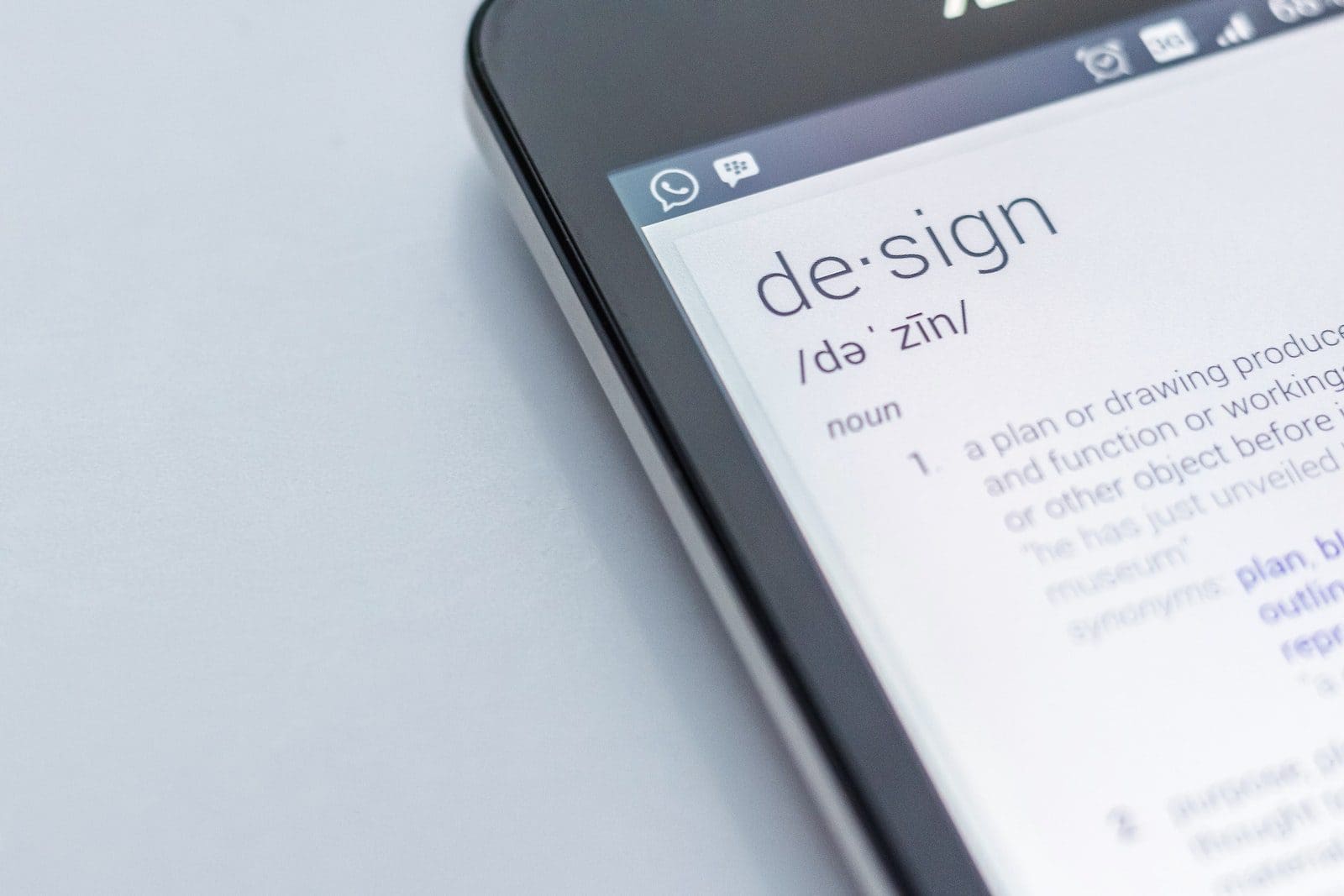
Wat is PFMEA?
PFMEA is een analysemethode voor processtoringsmodus en effectanalyse. Ook deze methode valt onder het faalwijze- en effectanalyseproces. Het detecteert alle mogelijke fouten die worden gemaakt tijdens de verwerking van een product of systeem.
Het is een methode die wordt gebruikt in het productproductieproces en die de mogelijkheid van een verwerkingsfout en de gevolgen daarvan vindt met behulp van een gedetailleerde rapportanalyse.
Het is een geïntegreerde tool die door alle soorten instellingen wordt gebruikt voor het controleren van verschillende mogelijke fouten die het falen van een systeem of product kunnen veroorzaken. Het detecteert ook de oorzaak van de storing door gegevens te verzamelen. Het wordt gestart of uitgevoerd voordat een product wordt verwerkt.
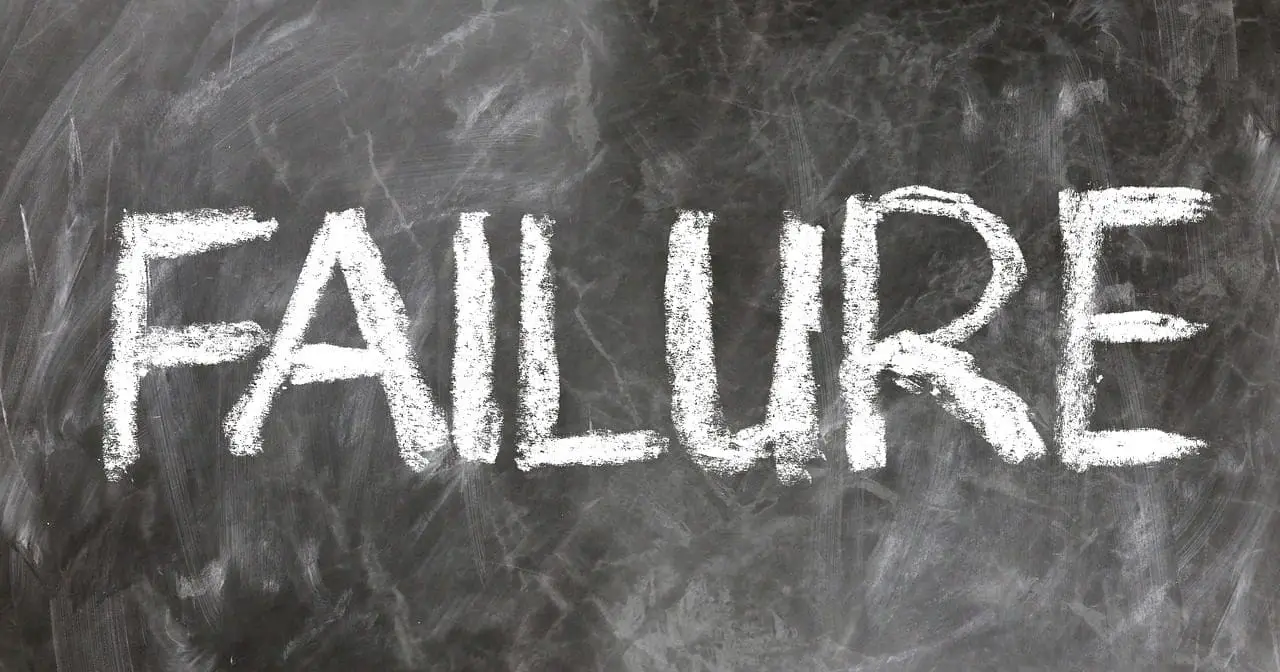
Belangrijkste verschillen tussen DFMEA en PFMEA
- DFMEA is volledig gerelateerd aan ontwerpkwesties. Het is een methode die wordt gebruikt om elke fout met betrekking tot de weergave van een systeem of product te analyseren. En PFMEA is volledig gerelateerd aan het proces met behulp waarvan een product of een systeem werkt. Het analyseert problemen met betrekking tot de verwerking.
- DFMEA legt vooral de nadruk op ontwerpgerelateerde aspecten van een product, en PFMEA legt de nadruk op productverwerking.
- PFMEA wordt gestart of uitgevoerd voordat een product wordt verwerkt. En DFMEA wordt geïnitieerd of uitgevoerd voordat een product of systeem wordt ontworpen.
- In DFMEA kunnen risico-items een wijziging in zowel het ontwerp als de verwerking veroorzaken. In PFMEA kunnen risico-items alleen een wijziging veroorzaken in de verwerking.
- DFMEA verkleint het risico op falen in het ontwerpproces en PFMEA verkleint het risico op falen in het productieproces door middel van een gedetailleerde rapportanalyse.
- https://www.sciencedirect.com/science/article/pii/S0957417409007039
- https://www.sciencedirect.com/science/article/pii/S0924013603005429
Laatst bijgewerkt: 11 juni 2023

Sandeep Bhandari heeft een Bachelor of Engineering in Computers van Thapar University (2006). Hij heeft 20 jaar ervaring op het gebied van technologie. Hij heeft een grote interesse in verschillende technische gebieden, waaronder databasesystemen, computernetwerken en programmeren. Je kunt meer over hem lezen op zijn bio pagina.
Dit is een ongelooflijk informatief artikel over DFMEA en PFMEA. Het legt grondig de verschillen tussen de twee uit en de betekenis van elk in het productontwikkelingsproces. Ik heb het gevoel dat ik veel inzicht heb gekregen door dit te lezen.
Ik ben het daar volledig mee eens, Bethany. Dit artikel heeft mijn begrip van deze concepten zeker verdiept.
De gedetailleerde uitleg van DFMEA en PFMEA was verhelderend, maar zou baat kunnen hebben bij voorbeelden uit de praktijk om het begrip te vergroten.
Je zit precies goed, Jrichards. Voorbeelden zouden de duidelijkheid en toepasbaarheid van deze methoden zeker vergroten.
Dit artikel lijkt de rol van DFMEA en PFMEA in productontwikkeling te simpel te maken. Er zijn meer complexiteiten bij betrokken die hier niet adequaat worden aangepakt.
Ik vond ook dat het enigszins ontbrak bij het behandelen van de volledige reikwijdte van deze analysemethoden, Irichardson.
Ik deel je perspectief, Irichardson. Het artikel lijkt een beperkte weergave van deze methoden te geven.
Het artikel geeft een uitgebreid overzicht van DFMEA en PFMEA, maar zou dieper kunnen ingaan op de procedurele aspecten en gedetailleerde casestudies.
Ik ben het met je eens, Chris. Real-world cases zouden praktisch inzicht bieden in de toepassing van deze methoden.
Hoewel het artikel een waardevolle bron is, lijkt het te ontbreken aan een diepgaande verkenning van de toepassingen van deze methoden in verschillende industrieën.
Ik ben het volledig met je eens, Gary. De specifieke toepassingen van DFMEA en PFMEA in verschillende sectoren zouden verrijkend zijn geweest.
Hoewel ik de gedetailleerde informatie in dit artikel op prijs stel, ben ik van mening dat de nadruk op deze methoden voorbijgaat aan andere belangrijke kwaliteitsborgingsprocessen bij productontwikkeling.
Dat is een terecht punt, Evie. Het zou nuttig zijn om de integratie van deze methoden met andere kwaliteitsborgingsprocessen te onderzoeken.
Ik ben het ermee eens, Evi. Hoewel DFMEA en PFMEA waardevol zijn, moeten ze deel uitmaken van een bredere kwaliteitsmanagementstrategie.
De vergelijking tussen DFMEA en PFMEA maakte de verschillen heel duidelijk. Het is een humoristische benadering van een technisch vakgebied!
Absoluut, Vhall. Het is niet zo dat we een vleugje humor zien in technische artikelen.
Ik kon het niet laten om te grinniken over de manier waarop de vergelijkingstabel zulke complexe concepten vereenvoudigde.
De uitgebreide vergelijkingstabel tussen DFMEA en PFMEA was bijzonder nuttig. Het verduidelijkt de verschillen en voordelen van elke methode zeer effectief.
Absoluut, Charlotte. Het is een geweldig naslagwerk voor iedereen die deze methoden in detail wil begrijpen.
Hoewel de inhoud informatief is, kan de toon van het artikel als overdreven technisch worden ervaren. Het toevoegen van een vleugje toegankelijkheid zou de aantrekkingskracht voor een breder publiek vergroten.
Ik ben het ermee eens, Lwalker. Als deze concepten op een toegankelijkere manier worden gecommuniceerd, wordt de inhoud inclusiever.
Absoluut, Lwalker. Bij dit soort artikelen is een balans tussen technische details en toegankelijkheid belangrijk.
Het onderscheid tussen DFMEA en PFMEA werd duidelijk verwoord, wat een samenhangend begrip opleverde. Het is prijzenswaardig hoe de belangrijkste verschillen naar voren werden gebracht.
Ik ben het daar volledig mee eens, Simpson. Het artikel heeft fantastisch werk geleverd door de nuances tussen de twee methoden te benadrukken.
Absoluut, Simpson. De duidelijkheid bij het onderscheiden van deze methoden was opvallend.